Click on the logo to learn about HIPERPAV
--
An application to simulate the impact of design, construction and weather factors on crack control
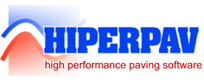
Download Demo |
Click here to download a comprehensive report on this topic
How Cracks Form
Early cracking is a complex interaction of a variety of seemingly unrelated factors. When all goes well on a project, cracks form at planned locations where contraction joints are placed in the slab. For most projects, transverse and longitudinal contraction joints are made by sawing the concrete with single-blade, walk-behind saws. For wide paving (generally greater than 8 m (24 ft), contractors sometimes elect to use span-saws that are able to saw the full-width in one pass. Each transverse and longitudinal saw cut induces a point of weakness where a crack will initiate, and then propagate to the bottom of the slab.
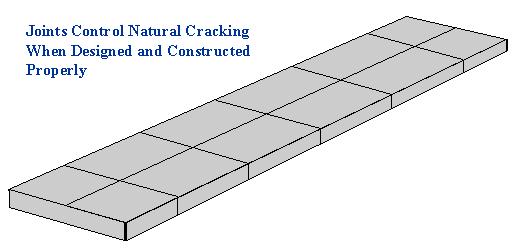
New concrete slabs crack whenever tensile stresses building up within the concrete overcome the concrete's tensile strength. The tensile stresses develop from restraint of the concrete's volume change at early ages, and restraint of bending from temperature and moisture gradients through the concrete. Early volume changes are associated with the concrete's drying shrinkage and temperature contraction.
In most cases, cracks first appear at large intervals, 10-45 m (30-150 ft), and then form at closer intervals over time. From this experience one may infer that restraint to volume change is the initial factor controlling cracking. Studies of plain pavements, 4-6 m (15-20 ft) transverse joint spacing support this inference. These studies show that intermediate sawed joints - normally required to control cracking from differentials - sometimes do not crack for several weeks to months after opening the pavement to traffic. However, this may not be true on every pavement, and it may be very difficult to determine whether restraint to volume change or restraint to gradients cause the first cracks.
Unfortunately, some concrete pavements do not crack at the saw cuts and instead crack at unplanned locations. The common terms for these early cracks are "random cracks" or "uncontrolled cracks." There are many reasons that uncontrolled cracks occur, and it is usually a challenging task to isolate the cause(s). However, experience in examining projects has led to identification of some consistent characteristics and causes.
Saw Timing
There is an optimum time to saw contraction joints in new concrete pavements, which is defined as the sawing window (Figure 1) (2,5). The window is a short period after placement when the concrete can be cut successfully before it cracks. The window begins when concrete strength is acceptable for joint sawing without excessive raveling along the cut. The window ends when significant concrete shrinkage occurs and induces uncontrolled cracking.
Under most normal weather conditions and for typical pavement designs the window will be long enough to complete sawing with excellent results. However, certain design features and weather conditions can considerably shorten the window (Table 1).
Orientation & Time of Crack Occurrence -- The orientation of uncontrolled cracks can indicate the possibility that sawing was too late. If a crack reverses direction, or develops in an unusual orientation, it may have initiated at the bottom of the slab and may have been influenced by high friction or bonding to the subbase (2). When an uncontrolled crack extends across the entire width of a paving slab, or begins and ends at a functioning joint, the possibility of late sawing remains. In most cases uncontrolled longitudinal cracks from late sawing will be in predictable locations as depicted in Figure 2A-C. Transverse cracks from late sawing are less predictable, but generally extend across the entire slab or traverse diagonally (Figure 2D).
Sometimes cracks continue to form well after paving and sawing are complete. In some cases these may be cracks that formed early and are simply becoming visible. In other cases, this is a clue that something is restraining or moving the concrete, which is creating tensile stresses that lead to further cracking.
Aggregate Condition Along the Crack Face -- Examining the faces from a core taken through an uncontrolled crack provides a clue to the time the crack occurred. Cracks that form below saw cuts usually develop after some reasonable strength development and will break through some coarse particles. If the crack travels around the coarse aggregate particles, it is most likely that the crack formed at a very early age, before the cement paste was able to bond sufficiently to the aggregates. For example, this may occur when the subbase contracts from a reduction in temperature and induces reflective cracks in the concrete at an early age. The bond strength between the cement paste and dirty, dusty or extremely hard coarse aggregate also may be low at an early age, which could also contribute to cracking around coarse particles.
Sawing Pop-Off Cracks -- At or near the end of the sawing window, cracks may form while the saw operator is making a cut. These cracks often occur as the saw progresses to within about 1 m (3 ft) of the free edge of the slab (Figure 2D). Pop-off cracks are an indication that sawing is too late for the prevailing conditions. There is a higher tendency for pop-off cracks if a high wind is blowing against the edge of the slab, accelerating evaporation and shrinkage. Experienced saw operators will orient the direction of sawing with the wind whenever possible.
Saw Cut Depth
The influence of the saw cut depth on the occurrence of early transverse cracking primarily depends on the time of the sawing (3). According to Zollinger, early-age sawing methods with sawing depths less than 0.25d (d=slab depth), should provide better crack control than conventional methods with depths of 0.25d or 0.33d. He cites that sawing sooner with early-age saws can take advantage of larger changes in the concrete's surface moisture content or surface temperature, which has been shown to induce cracking (2). Zollinger verified the effectiveness of early-age sawing methods with field experience on 330 mm (13 in.) plain concrete pavement, made with a variety of coarse aggregates, on granular soils. Further verification is necessary for crack control in plain concrete on stabilized subbases that induce more restraint.
Deeper saw cuts are necessary for conventional sawing equipment because the concrete is generally under more restraint than when sawed at earlier ages with early-age sawing equipment. Practical experience shows that transverse cuts from one-fourth to one-third the slab thickness (0.25d to 0.33d) will provide crack control under most circumstances for conventional sawing operations. However, there is little information to quantify the increased probability of uncontrolled cracking should the cut depths not meet a specified (0.25d or 0.33d) minimum depth. Okamoto attempted to determine the necessary transverse cut depth for conventional sawing equipment and operations (2). He concluded that there are too many confounding factors to develop a verified recommendation for transverse joints.
For longitudinal contraction joints, McCollough found that uniformity in concrete strength, slab thickness and cut depth should improve the probability of longitudinal crack control (6). According to his model, a saw depth of 0.25d controls longitudinal cracking with 98% reliability in mixtures containing crushed limestone aggregate, and with 86% reliability in mixtures containing river gravel. However, other experiences show that more factors also may be involved in longitudinal cracking. On one test pavement in Minnesota, sections on granular subbase had very little longitudinal cracking, while sections on asphalt or cement stabilized materials - that induce higher frictional restraint - had extensive longitudinal cracking (2). On all sections the contractor formed the longitudinal joint with a plastic-tape insert at a similar time and orientation during paving.
While it is not precisely proven that saw cut depth alone directly relates to occurrence of transverse or longitudinal cracking, it is a commonly specified factor. Currently 96% of state agencies require a cut depth of 0.25d for transverse contraction joints (7). We (American Concrete Pavement Association) recommend a depth of 0.33d for longitudinal contraction joints, and transverse contraction joints in highway pavements, and all pavements placed on stabilized subbase materials (1).
On projects where contractors use conventional diamond-bladed sawing equipment, shallow (less than 0.25d or 0.33d) saw cuts are often a symptom of late sawing rather than a direct cause of cracking through poor equipment set-up. When cracking is imminent near the end of the sawing window, saw operators may tend to push a saw too fast, causing the saw blade to ride up out of its full cut.
Another possible cause of shallow saw cuts are worn abrasive saw blades. During use, the diameter of an abrasive blade becomes progressively smaller as the abrasive cutting material wears away. Saw operators must closely monitor abrasive blade wear and replace worn blades to consistently meet depth requirements.
Weather & Ambient Conditions
The weather almost always has some role in the occurrence of uncontrolled cracking. Air temperature, wind, relative humidity and sunlight, influence concrete hydration and shrinkage. These factors may heat or cool concrete or draw moisture from exposed concrete surfaces. The subbase can be a heat sink that draws energy from the concrete in cold weather, or a heat source that adds heat to the bottom of the slab during hot, sunny weather.
Under warm sunny summer conditions, the maximum concrete temperature will vary depending on the time of day when the concrete is paved. Concrete paved in early morning will often reach higher maximum temperatures than concrete paved during the late morning or afternoon because it receives more radiant heat (Figure 3). As a result, concrete paved during the morning will generally have a shorter sawing window, and often will exhibit more instances of uncontrolled cracking.
After the concrete sets, uncontrolled cracking might occur when ambient conditions induce differential thermal contraction (2,8). Differential contraction is a result of temperature differences throughout the pavement depth. Research indicates that a sudden drop in surface temperature more than 9.5°C (15°F) can result in cracking from excessive surface contraction (2). This degree of temperature change is common year-round in arid climates, and possible in most other climates during the spring and fall when air temperatures drop significantly from day to night. Differential contraction also may occur when a rain shower cools the slab surface, or when the surface cools after removing insulating blankets from fast-track concrete.
Subbase
Stabilized subbases may induce uncontrolled cracking because of the high friction and, in some cases bonding, between the subbase and concrete slab. The friction or bond restrains the concrete's volume change (shrinkage or contraction), inducing higher stresses than might occur in concrete pavement on granular subbases. According to Okamoto, as the subbase friction increases, cracks occur from smaller drops in surface temperature than are necessary on low-friction subbases (2). This corresponds to field experiences on projects with cement-treated subbases, and asphalt-treated or cement-treated permeable subbases that were known to have bonded to the concrete pavement (9-11).
Cracks from bonding to the subbase are likely to initiate from the bottom of the slab and travel toward the slab surface, sometimes reflecting from shrinkage cracks in the stabilized subbase. Cracks from high friction can be erratic in orientation, sometimes reverse direction and seem to follow zones of restraint between the concrete and subbase (Figure 2G).
In addition to adding restraint, bonding or high friction between the pavement and subbase also will reduce the effective saw cut depth. For example, a typical 250-mm (10-in.) slab requires a 63 mm (2.5-in) saw cut to meet typical 0.25d requirements. If the slab bonds to a 100 mm (4-in.) stabilized subbase, the effective depth of the saw cut is only about 0.18d, which may not be adequate to control cracking with normal sawing equipment and timing.
To prevent bonding between the concrete and subbase requires the application of a bond-breaking medium. For lean concrete or econocrete subbases, current recommendations are for two spray applications of wax-based curing compound on the subbase surface (2,12). There are no standard or common bond-breaker recommendations for cement-treated subbases or asphalt-stabilized subbase materials. However, many cement-treated subbase specifications recommend a cutback asphalt for curing, that is sometimes believed to also serve as a bond-breaker. However, in some cases the treated subbase surface is disturbed by trimming prior to paving. After trimming the surface may be rough in certain locations creating an excellent surface for bonding. The ACPA recommends the application of two coats of wax-based curing compound before paving on cement-treated subbases.
Slag or very dry granular subbases also may contribute to uncontrolled cracking. Some contractors postulate that the slags draw moisture from the concrete pavement, which dries the lower portion of the slab before the middle or the top. This induces differential shrinkage in the reverse of surface drying from high winds. Most specifications for granular materials appropriately require moistening a granular subbase surface before placing any concrete. It is debatable whether typical subbase moistening efforts are practical or effective for slag subbase materials due to the high absorptive capacity of the aggregates.
Concrete Mixture
The internal temperature and moisture of concrete will influence the time available for joint sawing. The temperature relates to the concrete's strength gain and controls the ability to start sawing without raveling, and to finish sawing before the onset of cracking. Okamoto found that an easy way to determine the end of the sawing window is by monitoring the concrete surface temperature (2). He suggests that it is preferable to begin sawing when practicable, when the concrete sets enough to accept sawing, and to complete sawing before the surface temperature begins to fall since thermal contraction begins as the concrete temperature falls.
Higher concrete strength should enable the concrete to withstand more tensile stress when it first cools and undergoes temperature differentials. However, concrete mixtures that gain strength rapidly may have a shorter window for sawing than normal mixtures if the heat from hydration is high. These mixtures will experience a larger temperature differential than mixtures that gain strength more slowly and do not become as warm. It is not uncommon for concrete pavement temperatures to exceed 45 °C (113 °F) in summertime, particularly for fast-track concrete paving (5,8).
Mixtures containing certain fly ashes or lower quantities of portland cement can delay early age strength development in cooler weather. Depending on the air and concrete temperature, this could delay concrete setting and the ability to saw without excessive raveling. After setting, the time available for sawing before the onset of cracking may be much shorter than normal.
Concrete with granite and limestone coarse aggregate is less sensitive to temperature than concrete made from siliceous gravel, chert or slag aggregate. Granite and limestone have lower coefficients of thermal expansion than the other aggregates. Therefore, concrete made with granite or limestone is less temperature sensitive and generally allows a longer spacing between contraction joints without any additional chance of cracking. The influence of coarse aggregate was recognized many years ago, as seen in Table 2 showing spacing recommendations from 1955 (14). Interesting recent field tests show that cracks form at the saw cut sooner and more frequently with concrete made from river gravel than concrete made with crushed limestone (8).
Saw Blade Selection
Raveling usually occurs when sawing too soon, but it can also be caused by the saw equipment or saw blade. (14) A saw blade must be compatible with the power output of the saw, the concrete mixture, and the application. An improper saw blade will dull rapidly and can dislodge aggregate while trying to cut. In some cases switching to a different saw blade will correct the problem.
Plugging or clogging of the cooling water tubes on a diamond-bladed saw also may cause a raveled cut. Therefore it is important for saw operators to monitor the sawing equipment to determine if it is creating a raveled cut in concrete that is otherwise ready for sawing. Experienced saw operators rely on their judgment and the scratch test to make this determination, and then adjust their equipment so that it can operate correctly. The scratch test is the most common and one of the simplest tests that contractors use to determine when to begin sawing (14). The test requires scratching the concrete surface with a nail or knife blade, and then examining how deep the surface scratches. As the surface hardness increases the scratch depth decreases. In general, if the scratch removes the surface texture it is probably too early to saw without raveling problems.
Joint Spacing
Pavement with long transverse joint spacing may crack due to tensile stresses from temperature curling. Theoretical and practical studies of concrete pavement have determined that the optimal spacing between joints depends on the slab thickness, subbase stiffness, and concrete strength. Most state agencies specify transverse contraction joints in plain pavement at an interval between 4.5 and 6.1 m (15 and 20 ft.) (7). For granular subbase materials American Concrete Pavement Association recommends a maximum spacing of 24d, and for stabilized materials a maximum spacing of 21d (1). Still others recommend an even closer joint spacing based on maintaining the ratio of the slab length to the radius of relative stiffness below 5 (15,16). It is also important to check the transverse and longitudinal contraction joint spacing to see if it is within the limits recommended for different coarse aggregates.
Misaligned Dowels
The influence of dowel alignment on the development of early cracking is not well understood. If saw timing and saw cut depth are adequate, the misalignment of dowels can induce a crack away from a transverse joint if the dowels physically lock two slabs together and restrain their contraction (Figure 4). For this possibility, a crack must exist that extends below the saw cut. If there is no crack meeting the saw cut, then late sawing or subbase restraint is likely the cause of the uncontrolled crack. In some cases a crack may wander in and out of a saw cut above a doweled joint (Figure 2D). This also indicates that sawing was too late for the prevailing conditions.
An unanswered question is whether misalignment of dowels can ever induce a crack to form away from a saw cut if there is no crack extending from the cut. This would require that the dowels reinforce the concrete and mask the presence of the weakened plane. Since tied longitudinal contraction joints create significant restraint, without alarm for unusual cracking, it seems reasonable the same would hold true for misaligned dowels.
Rapid Surface Moisture Evaporation
It is important not to confuse cracks from restraint of the concrete at early ages, to plastic shrinkage cracks. Plastic shrinkage cracks are generally tight, about 0.3-0.6 m (1-2 ft) long, extend down about 25-100 mm (1-4 in.) from the surface, and form in parallel groups perpendicular to the direction of the wind at the time of paving. Plastic shrinkage cracking is a result of rapid drying at the concrete pavement surface, and therefore adequate curing measures are necessary to prevent their occurrence (5). Experience has shown that these cracks rarely influence the overall performance of a pavement.