Joint Sealants
Overview
The most widely accepted definition of a joint sealant today is a material that minimizes both infiltration of surface water and incompressible material into the joint system. Secondarily, sealants are also purported to reduce the potential for dowel bar corrosion by reducing entrance of de-icing chemicals. There are some errant claims that joint sealants prevent surface water from entering the joint system, but modern vacuum tests clearly show that no sealant will provide a perfectly watertight seal.
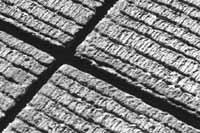
Joints Sealed with Self-Leveling Silicone
There is no doubt that water within a pavement's layers can contribute to subgrade or subbase softening and lead to pumping of subgrade or subbase fines under heavy channeled traffic. This degradation can result in loss of structural support, pavement settlement and/or joint faulting. Unfortunately, it is not practical to construct and continually maintain a completely watertight pavement. Therefore, the prevailing current practice by highway agencies is to use joint sealants to minimize passage of surface water through joints and also provide a permeable subbase to remove water from the pavement.
The other function of modern joint sealants is to prevent incompressible material from entering the joint reservoir. In some circumstances, incompressibles may contribute to spalling, and in some unusual cases, may induce pavement migration and "blow-ups." These problems are caused when incompressibles obstruct pavement expansion in hot weather and create compressive pressure along the joint faces.
History
Sealant use dates back to 1906, when heated tar was first placed between concrete slabs on projects in eastern cities, including Washington, D.C., and Summerville, Mass. Since then, engineers, manufacturers and contractors, have been working together to develop and refine seal materials. This has led to many improvements in the materials, as well as a shift in engineers’ expectations of these materials.
The first known national specification to require joint filling was the "Standard Specifications for Concrete Road and Street Pavements," developed in 1912 by the National Association of Cement Users (now the American Concrete Institute).
For many years, the term "joint fillers" described the purpose (and expectations) of materials placed in pavement joints. Filler materials were intended to keep incompressibles out of joints to prevent slab migration. Some specifications still refer to joint fillers.
In the 1970s, the expectations of joint fillers changed, and products were expected to minimize water infiltration too. The word "sealant" became more common, and in essence, defined the switch in expectations. Many engineers today think of sealant materials primarily for their ability to prevent water from passing through concrete pavement joints.
Joint Sealing Materials
Hot-pour liquid sealants have evolved after many years of research and development. They are quite different from the heated tar and bitumen placed in joints in the first half of the century, and have even changed from the materials used as recently as the 1970s.
Manufacturers have improved sealants’ adhesive qualities and now provide low-modulus materials with better elasticity than previous materials. About 25% of roadway agencies use hot-pour sealants in transverse joints of highway pavements. However, most of the hot-pour sealants sold by manufacturers today are used in low-volume concrete roads and highway pavement longitudinal joints.
Manufacturers introduced compression seals for pavement in the early 1960s. They differ from liquid sealants because they are manufactured ready for installation. Unlike liquid sealants, which stretch when the joint opens, preformed compression seals remain compressed throughout cycles of joint opening and closing. Therefore, their ability to remain in the reservoir and their long-term success depends primarily on the lateral pressure the seal exerts on the reservoir.
Compression seals also have changed over many years of refinement. Original web designs have been refined, and changes in the rubber compounds have improved durability of the seals. Compression seals are often called "neoprene" seals, for the seal’s primary elastomeric compound. Today, 21% of roadway agencies use compression seals in their highway pavement transverse joints.
Silicone sealants are field-poured cold liquids with a base ingredient of silicone polymer. Agencies began using these materials in the 1970s. Installation procedures are similar to those for hot-pour materials. Much care is necessary to clean and prepare the joint reservoir for silicone sealants. About 52% of roadway agencies currently use silicone sealant in their highway pavement transverse joints. While some changes have been made to silicone sealants from original materials, the materials in use today are quite similar to those first introduced. One alternate is self-leveling silicone sealant, which does not require tooling after pouring into the joint reservoir.
Joint Seal Design Strategies
Across all pavement applications, the most common joint sealant remains the hot-pour liquid sealant. Silicone sealants and compression seals have been adopted by some specifying agencies and are quite common in airport and highway pavements. The diagram below shows the various applications or reservoir designs used by state roadway agencies.

Of primary importance in liquid sealant installation are both cleanliness of the sidewalls and the shape of the sealant. The shape factor diagram below shows appropriate size recommendations for liquid (hot-pour or silicone) sealants. An appropriate compression seal width depends upon climate, installation temperature, concrete properties and joint spacing.

The time of installation of sealant materials depends upon the manufacturer's recommendations. Most manufacturers have specific recommendations, but the table below provides a summary.
Sealant Type |
Minimum Placement
Temperature |
Drying Period for Non-Fast Track Concrete |
Waiting Time to Open Sealed Joint to Traffic |
Asphalt Based Hot Pour |
50 deg. Farenheit |
7 days |
upon cooling |
PVC Coal Tar Based Hot Pour |
50 deg. Farenheit |
7 days |
upon cooling |
Polymeric Low Modulus Hot Pour |
40 deg. Farenheit |
7 days |
upon cooling |
Cold-Poured Silicone |
40 deg. Farenheit |
7 days |
30 min. |
Preformed Compression |
30 deg. Farenheit |
none |
immediate |
For more information, follow: