The U.S. Experience with Ultra-Thin Whitetopping
Introduction
Paved surfaces for roadways, both portland cement concrete and asphalt, must withstand very harsh conditions. Wheel loads from moving vehicles cause strains, stresses and deflections in the paved surface and underlying roadbed. Additionally, the pavement must endure environmental effects. Climatic changes cause temperature variations through the depth of the pavement, inducing internal stresses.
Asphalt properties, particularly stiffness, change with temperature. Moisture variations cause changes in foundation support. In many areas, freezing and thawing temperature cycles cause variations in foundation support and add additional stresses to the paved surface, particularly when moisture is also present.
Eventually, a pavement exhibits distress and requires rehabilitation. A variety of rehabilitation techniques have been developed. When properly applied at the appropriate time, rehabilitation techniques significantly extend the total life of concrete and asphalt pavements. One technique for rehabilitating distressed asphalt pavements is a concrete overlay. In North America, this technique is often referred to as "whitetopping." Whitetopping has been used in the United States since 1918 and routinely used since the mid-1970's.
It is a well-proven method of pavement rehabilitation. A new method of rehabilitating asphalt pavements was developed in the early 1990's. This technique requires bonding a relatively thin layer of concrete to the underlying asphalt to create a composite pavement section. In North America, this technique is called "ultra-thin whitetopping." While the technology is still developing, over 200 ultra-thin whitetopping sections have been built, primarily on low-volume roadways. Recently, however, thicker bonded concrete overlays of existing asphalt pavements have been built on three major highways in the U.S.
Whitetopping: Concrete Overlays of Existing Asphalt Pavement
Whitetopping is a pavement rehabilitation technique that has been evolving rapidly in the modern era of higher traffic volumes and heavier axle loadings. The first documented use of a concrete overlay over an existing asphalt roadway in the U.S. can be traced to 1918, when South 7th Street in Terre Haute, Indiana was whitetopped.
The technique was used sparingly in the 1950's and 1960's, primarily to upgrade the load-carrying capacity (both volume and structural capacity) of existing highways and rural roads. During the 1960's and 1970's, the State of California used 175 mm - 225 mm of plain (unreinforced) concrete overlay on several sections of existing asphalt highways. Three separate performance studies conducted from 1977 to 1981 independently concluded that these overlays provided excellent service. Many were in service with little or no rehabilitation for well over 20 years. A dramatic increase in the popularity of whitetopping emerged in the mid-1970's and continues today. The number of documented concrete overlays of asphalt pavements in the U.S. increased from 81 in 1982 to 189 in 1993. Whitetopping has been used to rehabilitate high-volume interstate expressways, rural highways, municipal streets, and rural county roadways. Since 1977, over 650 km of county roadways in the State of Iowa have been whitetopped. These roadways primarily serve as farm-to-market roadways in this agriculturally extensive region of the U.S.
Unbonded, Classical Whitetopping
Until 1991, most whitetopping projects in the U.S. did not purposely seek bond between the interface of the concrete overlay and the underlying asphalt surface. Rather, the existing asphalt serves as base for the new concrete overlay. Today, we refer to this technique as "conventional" or "classical" whitetopping, defined as: "A concrete overlay, usually of thickness of 100 mm or more, placed directly on top of an existing asphalt pavement."
Thin Bonded Whitetopping: A New Technology
While concrete overlays of existing asphalt roadways have a proven history of excellent performance in the U.S., a new technology emerged in the early 1990's which has dramatically expanded whitetopping technology and use. This rehabilitation technique purposely seeks to bond the concrete overlay to the existing asphalt. As a result, the concrete overlay and the underlying asphalt act as a composite section rather than two independent layers. This composite action significantly reduces the load-induced stresses in the concrete overlay. Therefore, the concrete overlay can be significantly thinner for the same loading as compared to a whitetopping section with no bond to the underlying asphalt.
Our First Experiment with Thin Bonded Whitetopping
The first thin bonded whitetopping experience in the U.S. was on a landfill disposal facility near Louisville, Kentucky beginning September 1991. The overlay was constructed on an existing asphalt access road that served 400 to 600 trucks per day, 5 ½ days per week. The existing asphalt pavement was milled to obtain a uniform profile.
The experiment consisted of two concrete thicknesses, 90 mm and 50 mm. The 90 mm section had joints at 1.83 m. The 50 mm test section had joints cut at 1.83 m in one area and 0.61 in another area. This location was chosen because it was viewed as an accelerated test.
The rate of truck loadings is 20 to 100 times greater than the number of trucks experienced by many lower volume roads, streets and parking areas in the United States. Though the test section was monitored for only 13 weeks, it carried truck traffic for approximately one year. Field, laboratory and theoretical study results indicated that bond developed between the underlying asphalt and new overlay. This bonding contributed significantly to the structural capacity of the new overlay.
Some of the other significant findings from the Louisville experiment included: 1. Bonded whitetopping, 50 to 90 mm thick, can carry traffic loadings typical on many low-volume roads, residential streets and parking lots. 2. Corner cracking was the predominant pavement distress. 3. Joint spacing has a significant effect on the rate of corner cracking. Pavement with joints spaced at 0.61 m showed considerably less cracking than pavement with 1.83 joint spacing for 50 mm thick whitetopping.
Ultra-Thin Whitetopping Emerges
The Louisville experiment with thin, bonded whitetopping showed the technique had value as a pavement rehabilitation option. However, "whitetopping" (in the classical or conventional approach) was an established concept in the U.S. Therefore, another term was needed to differentiate this new technology from classical whitetopping. Three features differentiated the whitetopping at the Louisville experiment from previous concrete overlays of asphalt:
(1.) The concrete overlay was substantially thinner than previous conventional whitetopping.
(2.) Bond between the concrete overlay and the underlying asphalt created composite action.
(3.) Short joint spacing significantly improved overlay performance. Based on these observations, the term "ultra-thin whitetopping" or "UTW" has been used in the U.S. to describe this technology.
Ultra-Thin Whitetopping Defined
When describing pavement thickness, terms such as "thick" and "thin" are relative and depend on the viewpoint and experience of the user. For UTW, a more definitive description is needed. Based on U.S. experience, ultra-thin whitetopping can be defined as: "A concrete overlay 50 mm to 100 mm thick with closely spaced joints bonded to an existing asphalt pavement."
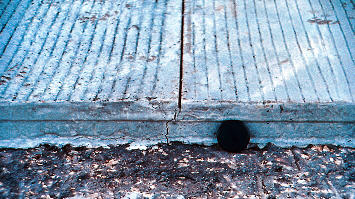
Effects of Bonding UTW Sections
In concrete pavement, cracks occur when stresses in the concrete exceed the concrete strength. Stresses are caused by vehicular loads and environmental conditions. Concrete, being much stronger in compression than tension, cracks when tensile stresses exceed the concrete's tensile strength. Bond between the concrete overlay and the underlying asphalt cause UTW to act as a composite section. Table 1 shows the theoretical tensile stress for a 75 mm thick concrete overlay of 100 mm of asphalt subject to a 36 kN wheel load (assuming typical values for the material properties of foundation support, concrete and asphalt). Effects of Joint Spacing on UTW Sections All pavement systems must absorb the energy of the applied load by either bending or deflecting. Traditional concrete pavements are designed to absorb the energy by bending and thus are made thick enough to resist stresses induced by bending.
|
Maximum tensile stress along free edge of concrete slab (MPa) |
Unbonded
Condition |
Bonded
Condition |
8.49 |
2.90 |
Maximum tensile stress near corner of concrete slab (MPa) |
Unbonded Condition |
Bonded
Condition |
6.12 |
3.68
|
Table 1 - Effects of bond (between the concrete overlay and the underlying asphalt) on the tensile stresses in the concrete overlay. Such bonding creates a composite pavement section, significantly reducing critical concrete overlay stesses.
For UTW sections, the joint spacing is intentionally kept short. The short joint spacing reduces the moment arm of the applied load and minimizes the stresses due to bending. In addition to load-induced stress, temperature and moisture variations through the concrete slab's depth cause internal stresses. The temperature gradient stresses are called "curling" stresses, while moisture gradient cause "warping" stresses. The short joint spacing also minimizes stresses due to curling and warping by decreasing the size of slab that can curl and warp. For the UTW overlays, the short joint spacing, in effect, transfers loads to the old flexible pavement through deflection rather than bending. (Figure 1)
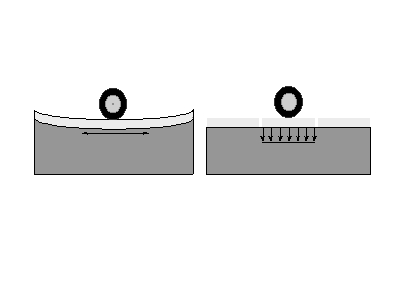
Figure 1: Shorter joint spacing reduces slab-bending. Wheel loads cause bending in concrete pavements with conventional joint spacing. In UTW, shorter joint spacing ca sues more transfer of wheel loads to the underlying asphalt through deflection.
Typical joint spacings that have performed well on UTW projects are somewhere between 0.6 and 1.5 m. Base on the U.S. experience, the recommended maximum joint spacing for UTW is 12 - 15 times the slab thickness in each direction. For example, for a 75 mm thick UTW, joints should be cut into concrete at 0.9 m to 1.25 m squares.
Effects of Asphalt Thickness
After surface preparation, there must be enough asphalt remaining to form a sufficient composite section that can carry the load. There must be enough asphalt to minimize concrete tensile stresses, and enough concrete to minimize asphalt strains. Based on U.S. experiences to date, it is recommended that the minimum asphalt thickness after milling exceed 75 mm.
Subsequent Experiences with UTW
A number of UTW projects were constructed shortly following the Louisville experiment. By 1997, over 200 projects had been built in North America. Figure 2 shows the increasing number of UTW projects from 1991 to 1997. The vast majority of these have been intersections and other locations where starting and stopping traffic has deteriorated the existing asphalt. Ultra-thin whitetopping has also been used to rehabilitate access or exit ramps to Interstate highways, entire sections of urban roadways, low-volume rural roads, bus lanes in municipal streets, general aviation aircraft parking aprons and automobile parking area.
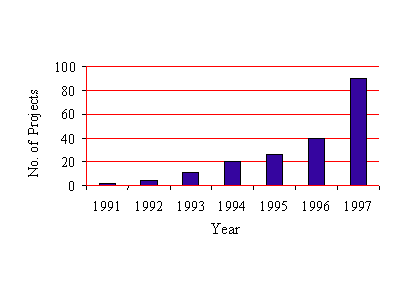
Figure 2 - Ultra-thin whitetopping technology continues to expand as the number of projects in the U.S. increases dramatically in the first seven years.
UTW - A Solution for Rutting Asphalt
While UTW has been used for a variety of applications, it is used primarily where rutting is a recurring problem in the existing asphalt. Rutting is the permanent deformation that occurs in some asphalt pavements from heavy wheel loads. Longitudinal troughs develop in the asphalt in the channelized wheel paths. In some severe cases, recurring rutting has caused asphalt pavements to be overlaid at intervals of two years or less. Many of the UTW overlays constructed in the U.S. from 1991 to 1997 were on such "problem pavements."
Constructing UTW Overlays Proper construction of ultra-thin whitetopping consists of four fundamental steps: 1. Prepare the asphalt surface by milling and cleaning, or water or abrasive blasting. 2. Place, finish, texture, and cure using conventional techniques and materials. 3. Saw joints to prevent cracking. 4. Open to traffic. A clean surface is required for proper bond. Milling the surface followed by cleaning improves bond because it exposes more of the aggregate of the asphalt pavement. The milling creates a rough surface the also enhances the bond between the two layers. If milling is not done, water or abrasive blasting should be used to clean the asphalt surface. When water blasting is used, the surface must be allowed to air dry before the concrete is placed.
Once a surface is cleaned it is important to keep it clean until the concrete overlay is placed. Dust, dirt and debris that falls or blows onto the asphalt surface must be removed. If the surface is cleaned on the day prior to paving, air cleaning may be required on the day of paving to remove dirt and dust. If traffic is allowed on the milled surface, the surface must be recleaned prior to paving. Paving UTW is no different from paving any other concrete pavement. Conventional slip-form and fixed-form pavers, as well as small equipment - such as vibrating screeds - have all been used successfully, without major modifications.
Typical concrete finishing and texturing procedures are appropriate for ultra-thin whitetopping. Proper curing is critical to avoiding shrinkage cracking in the concrete overlay and to prevent debonding between the asphalt and concrete. Because the overlay is a thin concrete slab, it has high surface area to volume ratio and can lose water rapidly due to evaporation.
Curing compound should be applied at twice the normal rate. Care must be used during application in order to avoid spraying curing compound on a prepared asphalt surface, which will decrease bonding. Joints should be sawed with lightweight saws as early as possible to control cracking. Saw-cut depth should be 1/4 - 1/3 of overlay thickness. Typically, the joints are not sealed. They have performed well without sealant because the short joint spacing minimizes joint movement. Performance to date shows no benefit from sealant use.
Concrete Mixture Proportions
The concrete mixture proportions selected for a particular project depends upon traffic conditions and opening-to-traffic requirements. A typical concrete mixture includes cementitious materials (cement and fly ash), coarse aggregate, fine aggregate, air entraining agent, and chemical admixtures (water reducers and/or plasticizers for a low water cement ratio). Many projects have included synthetic fibers. The fibers are added to increase the post-crack integrity of the panels. High early strength concrete mixtures capable of developing compressive strengths over 20 MPa within 24 hours have been used for a number of UTW projects.
Thin Composite Whitetopping for Major Highways
Ultra-thin whitetopping as conceived and developed in the early 1990's was intended for lower-volume roads, vehicular parking areas and light duty airports. The exceptionally thin overlay (as compared to classical whitetopping) and field performance on early projects (particularly the Louisville experiment) led to doubts about UTW's applicability to higher volume roadways, particularly Interstate highways. In 1997, however, three experimental projects were undertaken to adapt the concepts of UTW to higher-volume roadways.
Thin Composite Whitetopping - Not UTW
These three trials of new whitetopping technology on Interstate highways are an adaptation of ultra-thin whitetopping. While UTW is specifically defined to have a concrete overlay thickness of 50 - 100 mm, these new Interstate experiments have been constructed with concrete overlay thicknesses ranging from 100 mm to 175 mm. However, unlike conventional whitetoppings, these whitetopping sections are intentionally bonded to the underlying asphalt. Like UTW, joints are spaced at close intervals to reduce warping and curling stresses in the slab.
Thin Composite Whitetopping (TCW) - A New Technology
Thin composite whitetopping is being viewed as a new and emerging technology in the U.S. It is intended for higher volume roadways and airfields carrying a large number of heavy loads. Unlike UTW, overlay thickness is not an inherent part of the definition. Therefore, thin composite whitetopping can be defined as: "A concrete overlay intentionally bonded to an existing asphalt pavement to create a composite pavement section. Joints are spaced at close intervals to reduce stresses in the concrete overlay."
Three Experiments with Thin Composite Whitetopping
In 1997, three TCW projects were built in the U.S. on high-volume Interstate highways:
1.) I-495 near Boston, Massachusetts.
2.) I-20 near Bolton, Mississippi.
3.) I-94 near Otsego, Minnesota as part of the MnROAD pavement evaluation program.
All of these projects are being reviewed regularly for performance and reports are expected in the near future.
Mississippi's Thin Composite Whitetopping Research
The TCW research project on I-20 in Mississippi was undertaken as a partnering effort of the Mississippi Department of Transportation and the local concrete paving industry. The 1220 m long test section was built on a portion of existing asphalt pavement which had given unacceptable performance. The asphalt roadway had previously been rehabilitated with asphalt four times in 14 years. The outside (driving) lane of the 4-lane, divided Interstate highway contained asphalt ruts up to 50 mm deep, posing a danger to vehicles routinely traveling at 110 - 130 kilometers/hour. Conventional whitetopping is typically 250 mm - 300 mm thick for such conditions.
For this experiment, thin composite whitetopping sections that are 100 mm, 150 mm, and 200 mm thick will be evaluated. For this test, about 1220 m of the outside lane (3.6 m) was whitetopped. About half (610 m) of the evaluation section was overlaid with 100 mm of fiber-reinforced concrete. Polyolefin fibers, approximately 50 mm long, were added to the concrete at a rate of 15 kg/m3. Transverse joints in the 100 mm thick sections were spaced at 1.8 m, 4.6 m, 7.6 m and 12.2 m. A longitudinal joint was placed in the sections containing transverse joints at 1.8 m spacing resulting in 1.8 m x 1.8 m panels for this portion of the whitetopping. The remaining 610 m was built with plain concrete or concrete containing fibrillated polypropylene fibers at a rate of 0.9 kg/m3. Two whitetopping thicknesses were built - 150 mm and 200 mm. Joints are spaced transversely at 3.6 m in the 200 mm thick TCW section. In the 150 mm thick overlay, transverse joints are spaced at 1.8 m.
A longitudinal joint divides the 150 mm thick section into 1.8 m x 1.8 m panels. The 200 mm thick section is plain concrete. About 2/3 of the length of the 150 mm thick section contains fibrillated polypropylene fiber, while the remaining 1/3 is plain concrete. This TCW section was constructed using slipform paving equipment and met strict requirements for smoothness. A compressive strength of 17 MPa was required in 30 hours to facilitate rapid opening to Interstate traffic.
The Mississippi Department of Transportation, U.S. Army Corps of Engineers Waterways Experiment State and Mississippi Concrete Industries Association are evaluating the project at regular intervals. To date, good performance is reported. If performance meets expectations after about one year, Mississippi DOT will likely build a larger TWC test section of 13 to 16 km.
Conclusion
Concrete overlays of existing asphalt roadways is an established rehabiltiation technique in the United States. Referred to as "whitetopping", its popularity increased from the mid-1970's through the 1990's. In most cases, no attempt was made to adhere the concrete overlay to the existing asphalt pavement. No composite action between the two layers was accounted for in the concrete overlay design. Today, we refer to this technique as "classical" or "conventional" whitetopping. A new concrete overlay technique emerged in the 1990's.
Bond between the overlay and underlying asphalt was intentionally developed, creating a composite pavement system. When combined with short joint spacing, overlay thickness is considerably reduced (as compared to classical whitetopping). The result is "ultra-thin whitetopping" or "UTW". UTW overlays are 50 mm - 100 mm. thick. UTW was conceived for low-volume roads, general aviation aircraft facilities and vehicular parking areas. It has been used primarily used for sections of asphalt roadways where rutting is a recurring problem. Since its inception in 1991, over 200 UTW projects have been built. The fundamental concepts of UTW (bonded action, short joint spacing), but with somewhat greater overlay thickness, are now being evaluated on high-volume Interstate highways in the U.S.
These projects were built in 1997 in Massachusetts, Minnesota and Mississippi. We are referring to this technology as "thin composite whitetopping." While classical whitetopping is an established technology, we continue to learn and gain experience with ultra-thin whitetopping for lower volume roadways and thin composite whitetopping for high volume highways. We've clearly learned, however, that these techniques have opened new avenues for concrete overlays as a viable option for rehabilitating distressed asphalt roads. |